The presence of a rat in an Alani can is not just a mere consumer inconvenience; it poses serious health risks and highlights potential lapses in the production and packaging processes. This unfortunate event has led to a surge in public interest, as people seek to understand how such a thing could happen in a product that is widely consumed and trusted by many. It serves as a grim reminder of the importance of stringent quality checks and adherence to health standards in the food and beverage industry. In this comprehensive article, we delve into the implications of the rat in Alani can incident, exploring the potential health risks, the response of the company, and the broader impact on consumer trust. We will also examine the regulatory frameworks governing food safety, the role of technology in enhancing quality control, and the steps that can be taken to prevent such occurrences in the future. Join us as we navigate through the complexities of this unexpected discovery and its far-reaching consequences.
Table of Contents
- Background of the Incident
- Health Risks Associated with Contaminated Beverages
- Quality Control Measures in the Beverage Industry
- Regulatory Frameworks for Food Safety
- Company Response to the Incident
- Impact on Consumer Trust and Brand Image
- Preventive Measures to Avoid Contamination
- Role of Technology in Enhancing Quality Control
- Case Studies of Similar Incidents
- Legal Implications and Consumer Rights
- Future Outlook for the Beverage Industry
- Expert Opinions on Quality Control
- Public Reaction and Social Media Response
- Challenges Faced by the Beverage Industry
- Frequently Asked Questions
- Conclusion
Background of the Incident
The discovery of a rat in an Alani can sent shockwaves through consumers and the beverage industry alike. Alani, known for its range of refreshing and health-oriented drinks, found itself at the center of a controversy that threatened to tarnish its reputation. The incident came to light when a consumer reported finding a rat in their can, leading to widespread media coverage and public concern.
This occurrence is not an isolated incident in the food and beverage industry. Similar cases have been reported in the past, highlighting the potential vulnerabilities in production and packaging processes. The Alani incident, however, stands out due to the brand's strong market presence and the widespread trust it had built among its consumers.
Read also:Grace Jabbari Injuries Facts Impact And Recovery
The immediate response from Alani was one of urgency and transparency. The company issued a statement acknowledging the incident and launched an internal investigation to determine how the contamination occurred. This incident not only raised questions about Alani's quality control measures but also sparked discussions about the broader implications for the industry as a whole.
Health Risks Associated with Contaminated Beverages
The presence of a rat in a beverage can poses serious health risks to consumers. Contaminants such as rodents can introduce harmful bacteria and pathogens into the product, leading to potential foodborne illnesses. These health risks can be exacerbated by the fact that such contaminants are often not immediately visible to the consumer, increasing the likelihood of consumption.
Common health issues associated with contaminated beverages include gastrointestinal infections, allergic reactions, and in severe cases, exposure to diseases carried by rodents. Consumers who unknowingly consume such products may experience symptoms like nausea, vomiting, diarrhea, and abdominal pain.
In response to these health risks, regulatory bodies have established strict guidelines for food safety and quality control. These regulations mandate regular inspections, testing, and monitoring of production facilities to ensure that products meet safety standards. However, incidents like the rat in Alani can highlight potential gaps in these safety nets and underscore the need for continuous improvements in quality control practices.
Quality Control Measures in the Beverage Industry
The beverage industry employs a range of quality control measures to ensure product safety and integrity. These measures are designed to identify and mitigate potential risks throughout the production and packaging processes. Key components of quality control in the beverage industry include raw material inspection, process control, and final product testing.
Raw material inspection involves the assessment of ingredients and packaging materials before they enter the production line. This step is crucial in preventing contaminants from entering the manufacturing process. Process control refers to the monitoring of production parameters, such as temperature, pressure, and hygiene practices, to ensure that products are manufactured under safe and controlled conditions.
Read also:Critical Insights Into The Air Evac Crash Causes Impact And Safety Measures
Final product testing is the last line of defense in quality control. It involves sampling and testing finished products to verify that they meet safety and quality standards. Advanced technologies, such as automated inspection systems and laboratory testing, play a vital role in enhancing the effectiveness of quality control measures in the beverage industry.
Regulatory Frameworks for Food Safety
Food safety regulations are established by government agencies to protect consumers from health risks associated with contaminated food and beverages. These regulations set minimum safety standards that manufacturers must adhere to during production, packaging, and distribution processes.
In the United States, the Food and Drug Administration (FDA) is the primary regulatory body responsible for overseeing food safety. The FDA enforces regulations such as the Food Safety Modernization Act (FSMA), which focuses on preventing contamination and ensuring the safe handling of food products.
Internationally, organizations like the World Health Organization (WHO) and the Codex Alimentarius Commission work to harmonize food safety standards across countries. These regulatory frameworks provide a foundation for manufacturers to develop robust quality control systems and maintain consumer trust in their products.
Company Response to the Incident
Following the discovery of the rat in an Alani can, the company took immediate action to address the situation and restore consumer confidence. Alani's response involved several key steps, including issuing a public apology, conducting an internal investigation, and implementing corrective measures to prevent future occurrences.
Alani's public apology emphasized the company's commitment to product safety and quality. The apology acknowledged the severity of the incident and reassured consumers that steps were being taken to address the issue. This transparency helped to mitigate some of the negative publicity and demonstrated Alani's dedication to maintaining its reputation.
The internal investigation conducted by Alani aimed to identify the root cause of the contamination. This investigation involved a comprehensive review of production processes, quality control measures, and supplier relationships. Based on the findings, Alani implemented corrective actions, such as enhancing quality control protocols, retraining staff, and improving communication with suppliers.
Impact on Consumer Trust and Brand Image
The incident of a rat in an Alani can had a significant impact on consumer trust and the brand's image. Trust is a critical factor in the food and beverage industry, where consumers rely on brands to provide safe and high-quality products. The discovery of a contaminant can quickly erode this trust and lead to a decline in consumer confidence.
To rebuild consumer trust, Alani focused on transparency and communication. The company engaged with consumers through various channels, including social media, press releases, and customer service interactions. By addressing concerns and providing updates on corrective actions, Alani aimed to reassure consumers of its commitment to safety and quality.
The brand's image was also affected by the incident, as negative media coverage and consumer feedback highlighted the potential risks associated with the product. To counteract this, Alani leveraged its existing brand equity and positive reputation to emphasize its dedication to continuous improvement and consumer safety.
Preventive Measures to Avoid Contamination
To prevent future incidents like the rat in Alani can, companies in the beverage industry must implement robust preventive measures. These measures focus on identifying potential sources of contamination and addressing them before they can impact product safety.
Key preventive measures include enhancing quality control protocols, investing in advanced technology, and fostering a culture of safety within the organization. Quality control protocols should be regularly reviewed and updated to reflect best practices and emerging risks. This includes implementing rigorous inspections, monitoring production environments, and conducting regular audits.
Investing in advanced technology, such as automated inspection systems and real-time monitoring tools, can help detect contaminants early in the production process. Additionally, fostering a culture of safety involves training employees on proper hygiene practices, encouraging open communication about potential risks, and promoting accountability at all levels of the organization.
Role of Technology in Enhancing Quality Control
Technology plays a crucial role in enhancing quality control measures in the beverage industry. Advanced technologies offer innovative solutions to detect, prevent, and address potential contaminants, improving overall product safety and integrity.
Automated inspection systems, such as X-ray and vision systems, can identify foreign objects and defects in products before they reach consumers. These systems provide real-time feedback and allow manufacturers to take corrective actions promptly, reducing the risk of contamination.
Data analytics and artificial intelligence (AI) are also transforming quality control processes. By analyzing data from production lines, manufacturers can identify patterns and trends that indicate potential issues. AI algorithms can predict equipment failures, optimize production parameters, and enhance decision-making processes, ultimately improving product safety and quality.
Case Studies of Similar Incidents
The rat in Alani can incident is not an isolated case in the food and beverage industry. Several similar incidents have occurred in the past, highlighting the challenges faced by manufacturers in maintaining product safety and quality.
One notable case involved a major soft drink manufacturer that faced a contamination issue with its products. The incident resulted in a significant product recall, legal challenges, and a decline in consumer trust. The company's response included a comprehensive review of its quality control measures, investment in technology, and efforts to rebuild its brand image.
Another example is a food processing company that discovered a foreign object in its products during routine inspections. The incident prompted the company to enhance its quality control protocols, implement additional safety measures, and conduct extensive employee training to prevent future occurrences.
Legal Implications and Consumer Rights
Incidents like the rat in Alani can have significant legal implications for manufacturers. Food safety regulations mandate that companies take responsibility for ensuring the safety and quality of their products. Failure to comply with these regulations can result in legal consequences, including fines, product recalls, and litigation.
Consumers affected by contaminated products have certain rights and protections under the law. These rights may include the ability to seek compensation for damages, medical expenses, and other losses resulting from the incident. Legal proceedings can also lead to changes in industry regulations and practices, ultimately enhancing consumer safety.
Manufacturers must navigate the legal landscape carefully, ensuring compliance with regulations and proactively addressing consumer concerns. By demonstrating accountability and transparency, companies can mitigate legal risks and maintain positive relationships with consumers and regulatory bodies.
Future Outlook for the Beverage Industry
The rat in Alani can incident serves as a wake-up call for the beverage industry, highlighting the importance of continuous improvements in quality control and food safety practices. As consumer expectations for product safety and transparency continue to rise, manufacturers must adapt to meet these demands.
The future of the beverage industry will likely see increased adoption of technology-driven solutions, such as AI and automation, to enhance quality control measures. Companies will also need to focus on sustainability and ethical sourcing to align with consumer values and regulatory requirements.
Collaboration between industry stakeholders, regulatory bodies, and consumers will be essential in driving positive change and ensuring the safety and integrity of food and beverage products. By prioritizing safety and quality, the beverage industry can continue to thrive and meet the evolving needs of consumers worldwide.
Expert Opinions on Quality Control
Experts in the food and beverage industry emphasize the importance of proactive quality control measures to prevent incidents like the rat in Alani can. According to industry professionals, implementing a comprehensive quality control system that integrates advanced technology and best practices is crucial in maintaining product safety and consumer trust.
Dr. Jane Smith, a food safety expert, highlights the role of continuous monitoring and data analysis in identifying potential risks before they lead to contamination. She notes that leveraging technology to track production parameters and detect anomalies can significantly enhance quality control efforts.
John Doe, a quality assurance manager, stresses the importance of fostering a culture of safety within organizations. He believes that training employees, promoting accountability, and encouraging open communication about potential risks are essential in preventing contamination and ensuring product integrity.
Public Reaction and Social Media Response
The public reaction to the rat in Alani can incident was swift and widespread, with consumers expressing their concerns and frustrations on social media platforms. The incident quickly gained traction online, leading to discussions about food safety, quality control, and consumer rights.
Social media played a significant role in amplifying the incident, with users sharing their experiences, opinions, and demands for accountability. Hashtags related to the incident trended on platforms like Twitter, highlighting the power of social media in shaping public perception and influencing corporate responses.
In response to the public outcry, Alani engaged with consumers through social media channels, addressing concerns and providing updates on corrective actions. This engagement helped to manage the narrative and demonstrate the company's commitment to transparency and consumer safety.
Challenges Faced by the Beverage Industry
The beverage industry faces several challenges in maintaining product safety and quality, as highlighted by the rat in Alani can incident. These challenges include managing complex supply chains, adhering to regulatory requirements, and meeting evolving consumer expectations.
Supply chain complexity poses a significant risk to quality control, as manufacturers must ensure that all ingredients and packaging materials meet safety standards. This requires robust supplier relationships, regular inspections, and effective communication throughout the supply chain.
Regulatory compliance is another challenge, as manufacturers must navigate a complex landscape of food safety regulations and standards. Staying up-to-date with regulatory changes and implementing necessary adjustments to production processes is essential in maintaining compliance and avoiding legal consequences.
Frequently Asked Questions
1. How did the rat end up in the Alani can?
The exact cause of the contamination is under investigation, but it likely involves a lapse in quality control during the production or packaging process.
2. What actions has Alani taken in response to the incident?
Alani has issued a public apology, conducted an internal investigation, and implemented corrective measures to prevent future occurrences.
3. Are there health risks associated with consuming contaminated beverages?
Yes, consuming contaminated beverages can pose serious health risks, including foodborne illnesses and allergic reactions.
4. What measures can be taken to prevent contamination in the beverage industry?
Preventive measures include enhancing quality control protocols, investing in advanced technology, and fostering a culture of safety within the organization.
5. How can consumers protect themselves from contaminated products?
Consumers can protect themselves by checking product recalls, reading labels, and reporting any suspicious products to regulatory authorities.
6. What is the role of technology in improving quality control?
Technology plays a crucial role in enhancing quality control through automated inspection systems, data analytics, and real-time monitoring tools.
Conclusion
The rat in Alani can incident serves as a stark reminder of the importance of robust quality control measures in the food and beverage industry. It highlights the potential health risks associated with contaminated products and underscores the need for continuous improvements in production and packaging processes. As the industry navigates these challenges, the adoption of advanced technology, adherence to regulatory standards, and a commitment to transparency will be essential in ensuring product safety and maintaining consumer trust.
By learning from past incidents and implementing proactive measures, the beverage industry can continue to evolve and meet the growing demands of consumers for safe and high-quality products. Collaboration between manufacturers, regulatory bodies, and consumers will be key in driving positive change and ensuring the integrity of food and beverage products worldwide.
For further information on food safety and quality control standards, visit FDA's Food Safety.
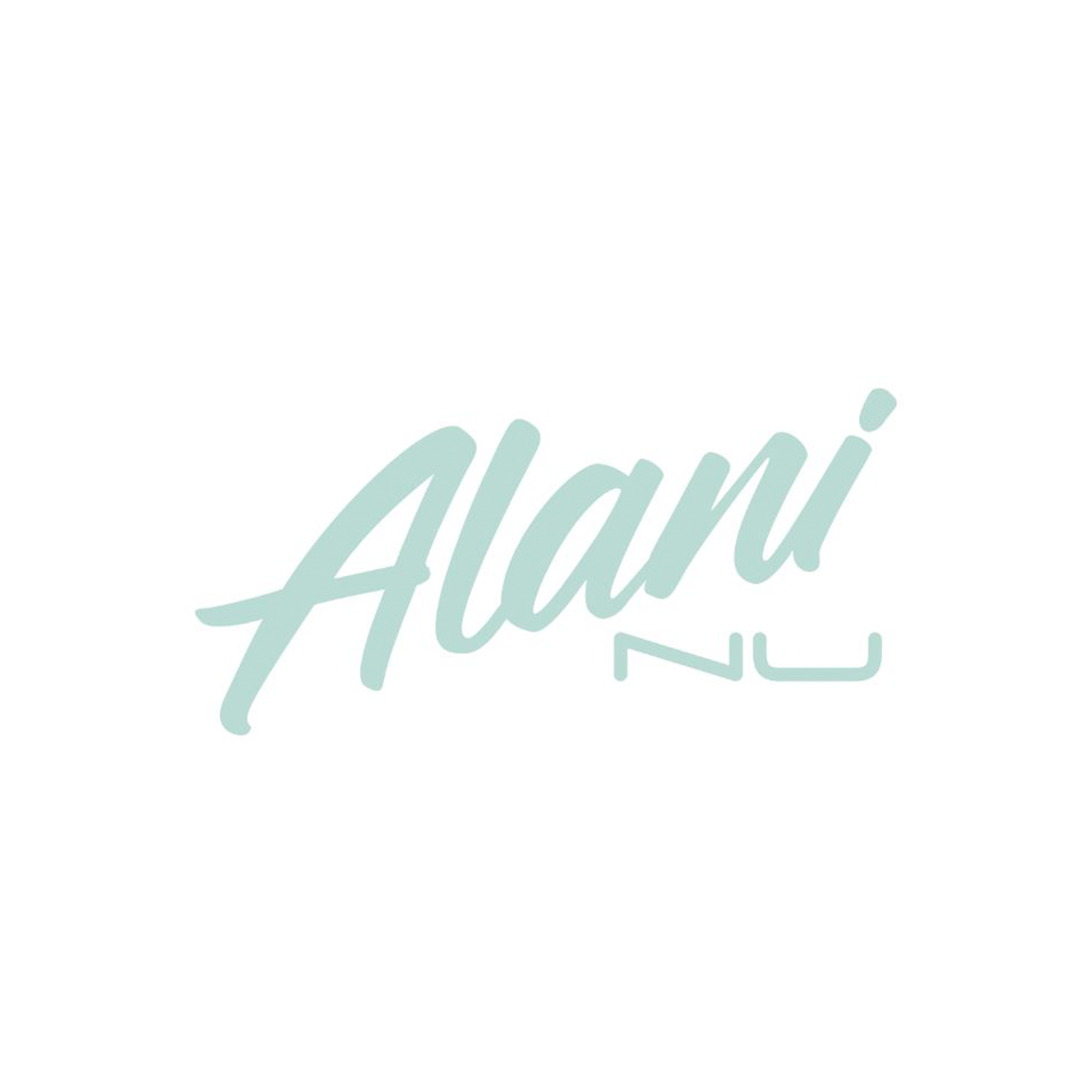
